Have you ever wondered what tires are made of and how these essential vehicle components are constructed to withstand such demanding conditions? Modern tires are sophisticated engineering marvels, combining various materials and compounds to create a product that ensures safety, performance, and durability on the road. From passenger vehicles to heavy-duty trucks, different types of tires require specific material compositions and construction methods to meet their intended purposes.
Today’s tire manufacturing involves a complex blend of natural and synthetic materials, carefully engineered to deliver optimal performance across various driving conditions. Whether you’re driving through rain-soaked highways or navigating snowy mountain passes, the composition of your tires plays a crucial role in keeping you safe and comfortable. Understanding the materials and construction methods used in modern tires can help you make informed decisions about your vehicle’s safety and performance.
What Raw Materials Are Used to Manufacture Tires?
The foundation of modern tire manufacturing lies in its carefully selected raw materials, each serving a specific purpose in the tire’s overall performance. Raw materials in tire production involve a sophisticated combination of natural and synthetic compounds, carefully formulated to create a product that can withstand extreme conditions while delivering consistent performance.
The manufacturing process begins with selecting high-quality materials that meet strict industry standards. Each component undergoes rigorous testing to ensure it meets specifications for durability, performance, and safety. According to the Tire Industry Association, modern passenger tires contain more than 200 different raw materials.
Leading tire manufacturers like Bridgestone invest significant resources in research and development to optimize their material selection and composition. This ongoing innovation helps improve tire performance while reducing environmental impact through more sustainable material choices.
How Is Natural Rubber Utilized in Tire Production?
Natural rubber remains a cornerstone of tire manufacturing, primarily sourced from rubber trees (Hevea brasiliensis) grown in Southeast Asia. The International Rubber Study Group reports that the tire industry consumes approximately 70% of the world’s natural rubber production.
Natural rubber provides essential properties such as high elasticity, excellent tear resistance, and superior heat dissipation capabilities. These characteristics make it particularly valuable for heavy-duty applications and specific tire components where durability is paramount. The processing of natural rubber involves multiple stages of refinement and treatment to achieve the desired properties.
According to Continental Tires, proper processing of natural rubber is crucial for maintaining consistent quality in tire production. The composition table below demonstrates the varying amounts of natural rubber used in different tire applications. Heavy-duty and specialized applications like aircraft tires require significantly higher percentages of natural rubber due to its superior strength and heat dissipation properties. This variation in natural rubber content directly influences the tire’s performance characteristics and intended use case.
Tire Type | Natural Rubber Content (%) | Primary Benefits |
---|---|---|
Passenger Car | 14-28 | Balance of performance and durability |
Light Truck | 27-33 | Enhanced load-bearing capacity |
Heavy Truck | 30-38 | Maximum durability and heat resistance |
Racing | 35-40 | Superior grip and heat management |
Aircraft | 40-45 | Extreme load and stress resistance |
What Percentage of a Tire Is Made from Synthetic Rubber?
Synthetic rubber components make up a significant portion of modern tire composition, typically ranging from 20% to 35% of the total rubber content. Unlike natural rubber, synthetic variants can be engineered to possess specific properties that enhance tire performance under various conditions.
The American Chemical Society highlights that synthetic rubber development has revolutionized tire manufacturing by providing consistent material properties and improved performance characteristics. Manufacturers carefully balance the ratio between natural and synthetic rubber to achieve optimal tire performance. This balance varies depending on the tire’s intended use, climate conditions, and performance requirements.
According to Goodyear’s Research Division, modern passenger tires typically contain multiple types of synthetic rubber, each serving a specific purpose. The development of new synthetic rubber compounds continues to advance, with researchers focusing on improving performance while reducing environmental impact. The Rubber Manufacturers Association reports that ongoing research aims to create more sustainable synthetic alternatives without compromising tire performance.
Types of Synthetic Rubber Used
Here are the primary types of synthetic rubber commonly used in tire manufacturing:
- Styrene-Butadiene Rubber (SBR) – Provides excellent abrasion resistance and aging properties, making up about 25-30% of passenger tire rubber content
- Polybutadiene Rubber (BR) – Enhances wear resistance and reduces rolling resistance, particularly beneficial for truck tires and high-performance applications
- Butyl Rubber – Creates an airtight inner liner, preventing air loss and maintaining proper tire pressure over time
- Ethylene Propylene Rubber (EPDM) – Offers superior weather resistance and is often used in sidewall compounds
- Neoprene – Provides excellent weather and ozone resistance, commonly used in specialty applications
Synthetic Rubber Type | Primary Function | Typical Content (%) | Best Application |
---|---|---|---|
SBR | Traction and Wear | 25-30 | Passenger Tires |
BR | Rolling Resistance | 15-20 | Truck Tires |
Butyl | Air Retention | 10-15 | Inner Liners |
EPDM | Weather Protection | 5-10 | Sidewalls |
Neoprene | Chemical Resistance | 3-5 | Special Purpose |
What Other Compounds and Chemicals Are Added to the Rubber?
The complex nature of tire manufacturing requires various additional compounds to enhance performance and durability. These chemical additives play crucial roles in determining the tire’s final characteristics. The Society of Chemical Industry emphasizes that modern tire compounds can contain up to 30 different chemical components.
Carbon Black
Carbon black serves as a primary reinforcing agent in tire compounds, significantly improving strength, wear resistance, and UV protection. The International Carbon Black Association notes that approximately 70% of all carbon black produced globally is used in tire manufacturing.
Key benefits of carbon black in tire production include:
- Enhances tensile strength and tear resistance
- Improves abrasion resistance and tread wear
- Provides UV protection to prevent rubber degradation
- Conducts heat away from the tire’s contact patch
- Contributes to overall tire durability
Silica
The introduction of silica as a reinforcing filler has revolutionized tire performance, particularly in wet conditions. Michelin’s Technical Center research shows that silica-enhanced compounds can reduce rolling resistance by up to 20% compared to traditional carbon black compounds.
Property | Carbon Black | Silica | Hybrid (Both) |
---|---|---|---|
Wet Grip | Good | Excellent | Very Good |
Rolling Resistance | Fair | Excellent | Good |
Wear Resistance | Excellent | Good | Very Good |
Cost Efficiency | Excellent | Fair | Good |
Manufacturing Ease | Excellent | Fair | Good |
Sulfur
Sulfur plays a critical role in the vulcanization process, creating strong chemical bonds between rubber molecules. The International Sulfur Association explains that this process transforms soft, sticky rubber compounds into durable, elastic materials essential for tire performance.
Modern tire manufacturing carefully controls sulfur content and vulcanization conditions to achieve specific performance characteristics. According to Yokohama’s Research Center, the amount of sulfur used typically ranges from 1% to 4% of the total compound weight, depending on the tire component and intended application.
The vulcanization process involves complex chemical reactions that determine key tire properties:
- Heat resistance and durability
- Elasticity and rebound characteristics
- Tensile strength and tear resistance
- Aging resistance and longevity
- Chemical resistance properties
Zinc Oxide
Zinc oxide serves as a crucial activator in the vulcanization process and provides additional benefits to tire compounds. The International Zinc Association reports that tire manufacturing consumes approximately 10% of global zinc oxide production.
Additive | Primary Function | Content Range (%) | Key Benefits |
---|---|---|---|
Zinc Oxide | Vulcanization Activator | 2-5 | Improved Processing |
Stearic Acid | Processing Aid | 1-2 | Better Mixing |
Antioxidants | Age Protection | 1-3 | Extended Life |
Accelerators | Cure Control | 0.5-2 | Faster Production |
Resins | Tack/Adhesion | 1-3 | Better Bonding |
How Are the Different Layers of a Tire Constructed?
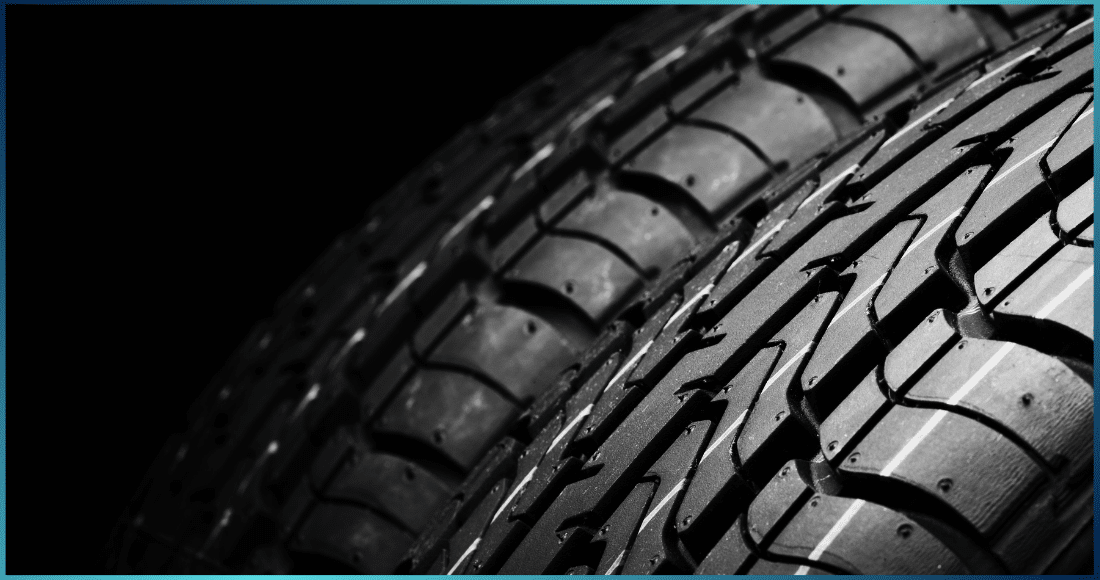
The construction of modern tires involves multiple layers, each serving specific functions in the tire’s overall performance. Tire construction techniques have evolved significantly since the early days of solid rubber wheels, as highlighted by the Smithsonian’s National Museum of American History.
According to Pirelli’s Technical Division, modern radial tire construction requires precise layering of various components to achieve optimal performance characteristics. Each layer must be carefully engineered and assembled to work in harmony with other components. The manufacturing process involves sophisticated equipment and quality control measures to ensure consistency.
The European Tyre and Rubber Manufacturers’ Association emphasizes that proper layer construction is crucial for tire safety and performance. Understanding the role of each layer can help appreciate the complexity and precision involved in tire manufacturing.
What Is the Purpose of the Tire Tread?
The tire tread represents the primary contact point between your vehicle and the road surface. Its design and composition significantly influence crucial performance aspects such as:
- Traction in various weather conditions
- Handling characteristics and stability
- Noise generation and comfort
- Water evacuation capabilities
- Overall tire longevity
The tread pattern and compound formulation work together to provide optimal grip and handling across a range of driving scenarios. Tread designs must balance competing factors like wet traction, dry handling, and tread life to meet the specific needs of each tire application.
Tread Patterns for Different Driving Conditions
Different driving conditions require specific tread patterns to optimize performance. The National Highway Traffic Safety Administration provides guidelines for selecting appropriate tread patterns based on driving conditions.
Tread Pattern | Best For | Key Features | Limitations |
---|---|---|---|
Symmetrical | All-Season | Long Life, Quiet | Average Performance |
Directional | Rain/Snow | Water Evacuation | Direction Specific |
Asymmetric | Performance | Balanced Handling | Higher Cost |
All-Terrain | Off-Road | Durability | Road Noise |
Winter | Snow/Ice | Maximum Traction | Faster Wear |
Selecting the right tread pattern for your driving needs can significantly impact your vehicle’s performance and safety. Consulting with a trusted tire professional can help ensure you choose the optimal tread design for your specific application and climate conditions.
How Does the Tire Carcass Provide Strength and Structure?
The tire carcass forms the foundation of modern tire construction, providing essential structural integrity and shape retention. According to the Tire and Rubber Association of Canada, the carcass typically consists of multiple layers of polyester or rayon cords embedded in rubber compounds, creating a robust yet flexible structure.
The design and construction of the carcass significantly influence tire performance characteristics. Research from the Japan Automobile Tyre Manufacturers Association shows that carcass construction can affect everything from ride comfort to fuel efficiency. Advanced manufacturing techniques ensure precise cord placement and optimal rubber coverage.
Modern carcass design must balance multiple competing factors, including durability, weight, and cost. The European Tire and Rim Technical Organization establishes guidelines for carcass construction to ensure safety and performance standards are met. Proper carcass design is essential for maintaining tire shape, supporting vehicle loads, and providing a stable foundation for the other tire components.
What Are the Steel Belts and How Do They Reinforce the Tire?
Steel belts provide crucial reinforcement to the tire structure, enhancing stability and handling characteristics. These belts consist of thin steel cords coated with brass to promote adhesion to rubber compounds. The Steel Manufacturers Association notes that tire-grade steel wire must meet stringent quality standards.
Key benefits of steel belt construction include:
- Enhanced tread stability under load
- Improved puncture resistance
- Better handling response
- Reduced rolling resistance
- Extended tread life through better wear distribution
The addition of steel belts revolutionized tire performance when introduced in the 1960s. Today, nearly all passenger and light truck tires incorporate steel belts for their superior reinforcement properties.
Arrangement of Steel Belts
Belt Layer | Primary Function | Typical Angle | Material Properties |
---|---|---|---|
First Layer | Stability | 65-70° | High Tensile Steel |
Second Layer | Support | 20-25° | Reinforced Steel |
Cap Ply | Protection | 0° | Nylon/Polyester |
Edge Protection | Durability | Variable | Hybrid Materials |
Joint Area | Integration | Mixed | Specialized Compounds |
The specific arrangement and composition of steel belts can vary depending on the tire application and manufacturer. However, the general principles of using angled steel layers for stability and support remain consistent across modern radial tire designs.
What Is the Inner Liner Made From and What Role Does It Play?
The inner liner serves as the air retention barrier in modern tubeless tires. Made primarily from butyl or halobutyl rubber compounds, this specialized layer prevents air loss and maintains proper inflation pressure. Lanxess Chemical Company research indicates that advanced inner liner compounds can reduce air loss by up to 30% compared to traditional materials.
Essential functions of the inner liner include:
- Maintaining consistent tire pressure
- Preventing moisture penetration
- Protecting steel components from corrosion
- Enhancing overall tire durability
- Contributing to fuel efficiency through proper inflation
Inner Liner Type | Air Retention | Cost Factor | Durability |
---|---|---|---|
Standard Butyl | Good | Moderate | Good |
Halobutyl | Excellent | High | Excellent |
Advanced Composites | Superior | Premium | Superior |
Nano-Enhanced | Ultimate | Very High | Outstanding |
The development of improved inner liner materials continues to advance, with manufacturers focusing on enhancing air retention while reducing weight. The Rubber Division of the American Chemical Society reports ongoing research into new compounds that could revolutionize air retention technology. Advancements in inner liner technology not only improve tire performance but also contribute to vehicle fuel efficiency and emissions reduction.
What Unique Materials Are Found in Specialty Tires?
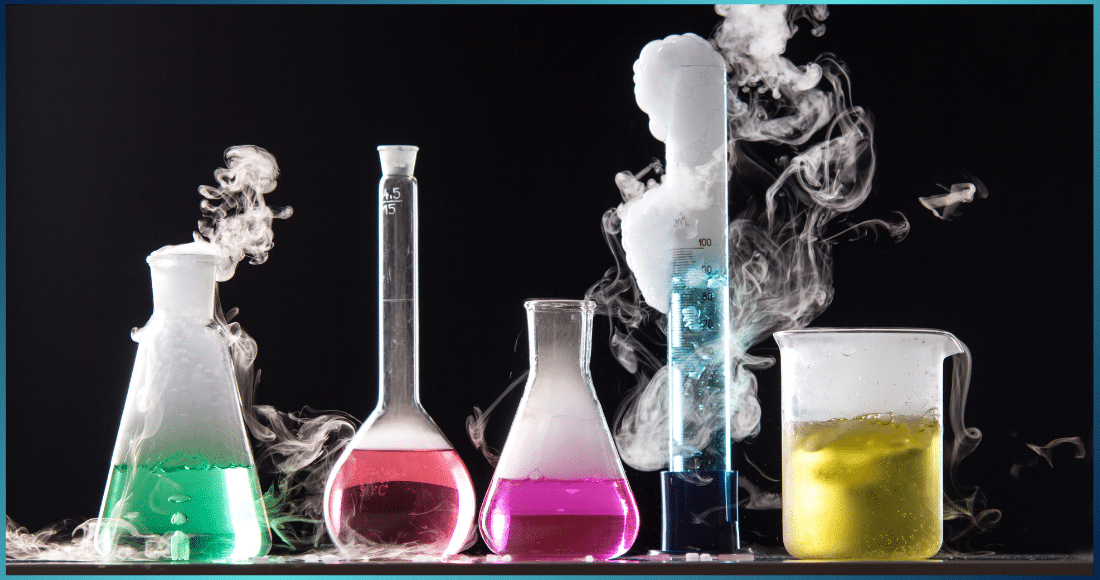
High-Performance Racing Tires
Formula One tire technology represents the pinnacle of tire engineering, utilizing specialized compounds and construction methods. According to Pirelli Motorsport, F1 tires contain unique materials that maximize grip and performance under extreme conditions.
Key differences in F1 tire composition include:
- Ultra-soft compound formulations for maximum grip
- Specialized reinforcement materials for high-speed stability
- Advanced heat-management compounds
- Unique tread patterns for specific track conditions
- Sophisticated internal structure for precise handling
Component | Regular Tire | F1 Tire | Performance Impact |
---|---|---|---|
Tread Compound | Durable | Ultra-Soft | Maximum Grip |
Internal Structure | Standard | Reinforced | High-Speed Stability |
Temperature Range | -20°C to 70°C | 90°C to 130°C | Optimal Performance |
Lifespan | 50,000+ km | 100-200 km | Race Specific |
Weight | 8-15 kg | 9-10 kg | Precise Engineering |
Airless Tire Technology
The development of airless tire technology represents a significant innovation in tire engineering. These revolutionary designs eliminate the need for air pressure maintenance while providing comparable performance to traditional pneumatic tires. The United States Patent and Trademark Office shows numerous patents related to airless tire technology, indicating significant ongoing innovation in this field.
Michelin Tweel Technology
Michelin’s revolutionary Tweel design incorporates flexible spokes made from composite materials that provide both support and shock absorption. Key features include:
- Composite spoke design for load support
- Specialized shear beam construction
- Advanced polymer materials
- Integrated tread design
- Modular replacement capability
Bridgestone Air-Free Concept
Feature | Advantage | Material Used | Development Status |
---|---|---|---|
Spoke Design | Load Distribution | Thermoplastic Resin | Commercial Testing |
Tread Band | Wear Resistance | Special Rubber Compound | Production Ready |
Support Ring | Structure Integrity | Composite Materials | Advanced Testing |
Connection Points | Durability | Reinforced Polymers | Optimization Phase |
Surface Contact | Performance | Enhanced Rubber | Final Development |
The potential benefits of airless tire technology include reduced maintenance, improved puncture resistance, and enhanced environmental sustainability through reduced waste and improved fuel efficiency. As research and development continue, airless tire designs may become a viable alternative for a wide range of applications in the future.
Aircraft Tire Specifications
Aircraft tire technology represents the ultimate in high-performance tire engineering. These specialized tires must withstand extreme loads, speeds, and temperature variations while maintaining absolute reliability. The Federal Aviation Administration mandates strict requirements for aircraft tire construction and performance.
Aircraft tires incorporate multiple reinforcement layers and specialized rubber compounds. According to Boeing’s Technical Journal, modern aircraft tires can withstand loads of up to 38 tons and speeds exceeding 200 mph during takeoff and landing. The manufacturing process for aircraft tires involves extensive quality control measures and testing. The Aerospace Industries Association reports that each tire undergoes multiple inspections and stress tests before certification.
Specialized Rubber Compounds in Aviation
Aircraft tire compounds must meet unique performance requirements:
- Extreme temperature resistance (-50°C to +200°C)
- Superior load-bearing capacity
- Exceptional burst resistance
- High-speed capability
- Advanced wear resistance characteristics
Property | Commercial Tire | Aircraft Tire | Military Aircraft |
---|---|---|---|
Load Rating | 1-2 tons | 15-38 tons | 20-45 tons |
Speed Rating | 240 km/h | 400 km/h | 450+ km/h |
Pressure | 30-35 psi | 200-250 psi | 300-350 psi |
Reinforcement | 2-3 layers | 15-20 layers | 20-25 layers |
Temperature Range | -20° to 70°C | -50° to 200°C | -60° to 250°C |
The extreme operating conditions and critical safety requirements of aircraft tires necessitate the use of highly specialized materials and construction techniques. Continuous research and development efforts aim to further improve aircraft tire performance, safety, and efficiency.
How Has Tire Composition Evolved Over Time?
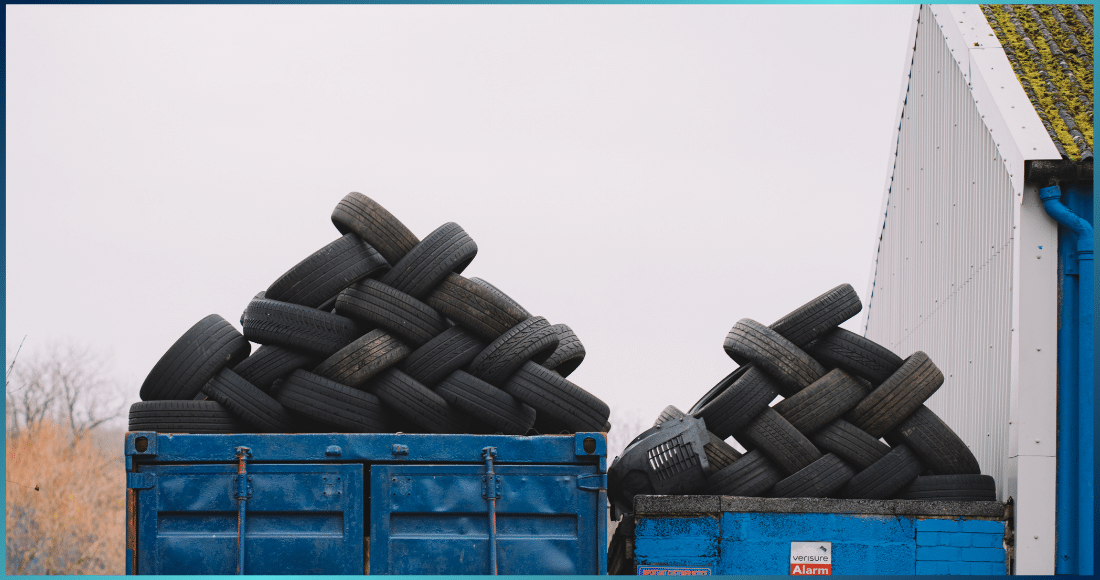
The evolution of tire materials reflects continuous technological advancement and changing market demands. The Rubber Division of the American Chemical Society documents how tire composition has transformed from simple rubber compounds to sophisticated engineered materials.
Early tire development focused primarily on natural rubber applications. The National Museum of American History chronicles how the discovery of vulcanization by Charles Goodyear in 1839 revolutionized the industry. Modern tire composition continues to evolve with increasing emphasis on performance and sustainability. Research from the World Business Council for Sustainable Development shows significant progress in developing eco-friendly tire materials.
Early Tire Materials and Construction
The journey of tire materials begins with simple natural rubber compounds. Key historical developments include:
- Natural rubber harvested from rubber trees
- Cotton and linen fabric reinforcement
- Basic carbon black compounds
- Early synthetic materials during WWII
- Introduction of steel-belted radial construction
Time Period | Primary Materials | Key Innovation | Impact |
---|---|---|---|
1800s | Natural Rubber | Vulcanization | Basic Durability |
Early 1900s | Fabric + Rubber | Cord Construction | Improved Strength |
1940s | Synthetic Rubber | War Innovation | Material Diversity |
1960s | Steel Belts | Radial Design | Modern Standard |
2000s | Silica Compounds | Green Technology | Efficiency Focus |
Synthetic Rubber Revolution
The development of synthetic rubber technology marked a pivotal moment in tire manufacturing history. According to the American Institute of Chemical Engineers, World War II necessitated rapid advancement in synthetic rubber research when natural rubber supplies were restricted.
The introduction of synthetic rubber provided manufacturers with greater control over material properties. The Society of Chemical Industry documents how synthetic rubber development enabled tires to meet increasingly demanding performance requirements across various applications. Research from DuPont’s Historical Archives shows that synthetic rubber innovations led to significant improvements in tire durability and performance characteristics.
Future Tire Material Innovations
Next-generation tire compounds focus on sustainability and enhanced performance. Key areas of development include:
- Bio-based synthetic rubber alternatives
- Nano-engineered reinforcement materials
- Smart compounds with self-healing properties
- Renewable resource-derived materials
- Advanced polymer composites
These innovative material technologies aim to reduce the environmental impact of tire production while simultaneously improving tire performance, safety, and durability.
Alternative Sources of Natural Rubber
Source Type | Development Stage | Advantages | Challenges |
---|---|---|---|
Guayule Plant | Commercial Trials | Desert Growth | Scale-up Costs |
Russian Dandelion | Research Phase | Cold Climate | Extraction Process |
Synthetic Biology | Early Development | Controlled Production | Technology Gaps |
Recycled Materials | Implementation | Sustainability | Quality Control |
Hybrid Sources | Testing | Versatility | Complex Processing |
Eco-Friendly Materials to Reduce Petroleum Usage
The push toward sustainable tire manufacturing has led to innovative material developments. The Environmental Protection Agency reports significant progress in reducing the environmental impact of tire production through new material technologies.
Key sustainable innovations include:
- Plant-based processing oils
- Recycled carbon black
- Bio-based reinforcing fillers
- Renewable polymer systems
- Energy-efficient curing agents
As environmental concerns continue to drive tire industry research and development, we can expect to see an increasing adoption of sustainable materials and manufacturing practices in the coming years.
What Are the Environmental Impacts of Tire Materials?
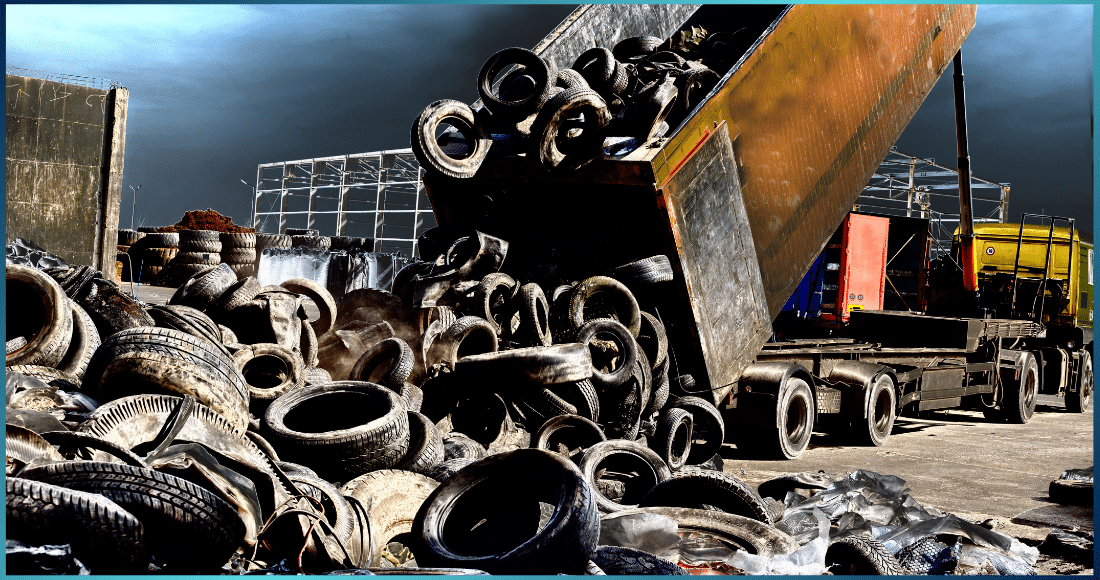
Understanding the environmental footprint of tire materials has become increasingly important. Research from the World Wildlife Fund highlights the significance of sustainable tire production in reducing global environmental impact.
The tire industry’s environmental impact extends beyond manufacturing. According to the Environmental Defense Fund, the entire lifecycle of tire materials must be considered when assessing environmental effects. Major environmental considerations include:
- Raw material sourcing and processing
- Manufacturing energy consumption
- End-of-life disposal methods
- Microplastic generation during use
- Carbon footprint throughout lifecycle
Addressing these environmental challenges requires a comprehensive approach that involves material innovation, process optimization, and end-of-life management strategies.
Petroleum Consumption in Tire Production
Petroleum consumption in tire manufacturing remains a significant environmental concern. According to the U.S. Department of Energy, producing a standard passenger tire requires approximately 7 gallons of oil, with about 5 gallons used in the tire materials and 2 gallons consumed during the manufacturing process.
The tire industry’s reliance on petroleum-based materials has sparked innovation in alternative materials. Research from MIT’s Materials Science Department indicates that emerging technologies could reduce oil consumption in tire production by up to 40% over the next decade. Current efforts focus on reducing petroleum dependency through advanced material science. The Natural Resources Defense Council emphasizes the importance of developing sustainable alternatives to traditional petroleum-based materials.
Sustainability Initiatives in Tire Manufacturing
The push for environmental responsibility has led major tire manufacturers to launch comprehensive sustainability programs. Key initiatives include:
- Development of renewable material sources
- Energy-efficient manufacturing processes
- Water conservation programs
- Waste reduction strategies
- Circular economy approaches
These initiatives aim to minimize the environmental impact of tire production while also improving operational efficiency and cost-effectiveness.
Low-Rolling Resistance Compounds
Technology | Fuel Savings | CO2 Reduction | Implementation Cost |
---|---|---|---|
Advanced Silica | 3-5% | 4-6 g/km | Moderate |
Nano-Materials | 5-7% | 6-8 g/km | High |
Bio-Based Oils | 2-4% | 3-5 g/km | Low |
Hybrid Compounds | 4-6% | 5-7 g/km | Moderate-High |
Smart Polymers | 6-8% | 7-9 g/km | Very High |
Increased Usage of Renewable Natural Rubber
Leading manufacturers are implementing sustainable rubber sourcing practices. The Forest Stewardship Council certifies rubber plantations that meet strict environmental and social standards, promoting responsible rubber production. Sustainable rubber sourcing not only reduces deforestation and biodiversity loss but also supports local communities and improves supply chain transparency.
End-of-Life Tire Management
Tire recycling technology continues to advance, offering new possibilities for end-of-life tire management. The Rubber Manufacturers Association reports that over 80% of scrap tires in the United States are now recovered for beneficial uses.
Modern tire recycling applications include:
- Ground rubber for sports surfaces
- Construction materials
- Road surface modifications
- Energy recovery systems
- Agricultural applications
Recycling Method | Environmental Impact | Economic Viability | Market Demand |
---|---|---|---|
Shredding | Positive | High | Strong |
Devulcanization | Very Positive | Moderate | Growing |
Pyrolysis | Mixed | Variable | Emerging |
Cryogenic Processing | Positive | High | Moderate |
Chemical Recovery | Very Positive | Low | Developing |
Effective end-of-life tire management not only reduces environmental pollution but also conserves valuable resources and creates new economic opportunities. Continued research and investment in tire recycling technologies will be crucial for addressing the global challenge of scrap tire accumulation.
What Brands Manufacture Their Tires in the United States?
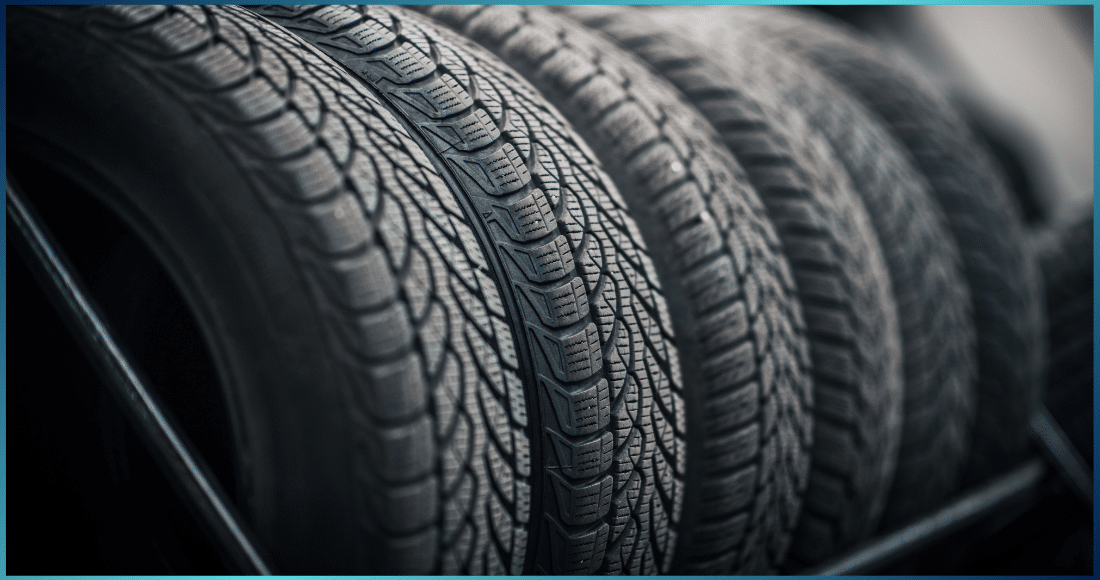
The domestic tire manufacturing industry plays a crucial role in the American economy. According to the U.S. Department of Commerce, tire production contributes significantly to manufacturing employment and economic growth across multiple states.
Manufacturing facilities require substantial investment in equipment and technology. The Bureau of Labor Statistics reports that modern tire plants employ thousands of skilled workers and utilize advanced automation systems to maintain quality and efficiency. These facilities also contribute to local economies through supplier networks and support services. Research from the Economic Policy Institute shows that each tire manufacturing job supports approximately 2.4 additional jobs in related industries.
Major U.S. Tire Manufacturers
Goodyear
Goodyear’s American operations represent a significant portion of domestic tire production. Their facilities include:
- Multiple state-of-the-art manufacturing plants
- Advanced research and development centers
- Specialized testing facilities
- Distribution networks
- Technical training centers
Facility Location | Production Capacity | Specialization | Employment |
---|---|---|---|
Akron, OH | Innovation Center | R&D/Testing | 3,000+ |
Topeka, KS | 6M tires/year | Commercial | 1,600+ |
Danville, VA | 8M tires/year | Passenger | 2,200+ |
Fayetteville, NC | 40K tires/day | Light Truck | 2,900+ |
Buffalo, NY | Technical Center | Development | 800+ |
Cooper
The Cooper Tire manufacturing network maintains several strategic locations across the United States. Their domestic operations focus on:
- High-performance tire production
- Custom manufacturing capabilities
- Quality control systems
- Market-specific designs
- Regional distribution
Cooper’s U.S. manufacturing presence demonstrates a strong commitment to domestic production and local job creation.
Michelin
Michelin’s U.S. presence includes multiple manufacturing facilities and research centers. Their commitment to American manufacturing involves:
- Sustainable production practices
- Advanced automation systems
- Workforce development programs
- Environmental initiatives
- Community engagement
Michelin’s investments in U.S. manufacturing not only support the domestic economy but also drive innovation and technological advancement in the tire industry.
Domestic Production Statistics
The domestic production ratio varies by tire category and market segment. According to the U.S. International Trade Commission, approximately:
- 45-50% of passenger tires
- 55-60% of light truck tires
- 70-75% of commercial truck tires
- 80-85% of specialty tires
Market Segment | Domestic Production | Import Share | Growth Trend |
---|---|---|---|
Passenger | 45-50% | 50-55% | Stable |
Light Truck | 55-60% | 40-45% | Growing |
Commercial | 70-75% | 25-30% | Increasing |
Specialty | 80-85% | 15-20% | Expanding |
Comparison of Domestic and Imported Tires
Quality standards and material specifications remain consistent regardless of manufacturing location. The National Highway Traffic Safety Administration enforces uniform safety and performance requirements for all tires sold in the United States.
Key comparisons include:
- Raw material sourcing practices
- Quality control procedures
- Manufacturing technology
- Environmental compliance
- Labor standards
While there may be differences in production costs and supply chain logistics, consumers can be confident that tires manufactured in the U.S. meet the same rigorous standards as their imported counterparts.
Final Thoughts
The materials and construction methods used in modern tires represent a remarkable blend of science, engineering, and craftsmanship. From the careful selection of raw materials to the precise layering of components, every aspect of tire design and manufacturing plays a crucial role in ensuring safety, performance, and durability on the road.
As the tire industry continues to evolve, we can expect to see even more innovative material developments and construction techniques aimed at improving tire performance while reducing environmental impact. The ongoing push for sustainability is driving research into bio-based materials, recycled content, and eco-friendly manufacturing processes. At the same time, advancements in nanotechnology, smart materials, and data-driven design are opening up new possibilities for enhancing tire safety, efficiency, and connectivity.
For consumers, understanding the main components and materials used in modern tires can help inform purchasing decisions and promote proper tire maintenance. By selecting tires that are well-suited to their specific driving needs and conditions, and by ensuring that those tires are properly inflated and maintained, drivers can optimize performance, safety, and longevity while minimizing environmental impact.
Ultimately, the future of tire technology will be shaped by a complex interplay of factors, including consumer demands, regulatory requirements, technological advancements, and sustainability imperatives. As manufacturers continue to push the boundaries of what is possible with tire design and materials, we can look forward to a new generation of tires that are smarter, safer, and more sustainable than ever before.
Discover the fascinating world of modern tire technology! Learn about the innovative materials and construction methods used to keep you safe on the road. Explore now!