Pneumatic tires have revolutionized the way vehicles move across various surfaces, offering superior comfort, safety, and performance compared to other types of tires. In the diverse world of tire technology, understanding the different types of tires available is crucial for making informed decisions about your vehicle’s needs. Whether you’re driving a car, riding a bicycle, or operating heavy machinery, the right tire choice can significantly impact your experience and safety on the road.
As we delve into this comprehensive guide, you’ll discover how these remarkable components work, their essential features, and why they’ve become the standard choice for most vehicles today. From their humble beginnings as a solution to uncomfortable rides to their current status as highly engineered products, pneumatic tires represent one of the most significant innovations in transportation history. Let’s explore their fascinating world and understand how they contribute to modern mobility. Understanding the intricacies of pneumatic tire design and function empowers vehicle owners and operators to make well-informed decisions regarding tire selection, maintenance, and replacement, ultimately ensuring optimal performance, safety, and efficiency in their specific applications.
What is the Definition of a Pneumatic Tire?
A pneumatic tire is an engineered rubber component that uses compressed air to support a vehicle’s weight while providing crucial functions like traction, shock absorption, and directional stability. These remarkable inventions have become an integral part of modern transportation, fundamentally changing how vehicles interact with various surfaces. The term “pneumatic” comes from the Greek word “pneumatikos,” meaning “of wind” or “of air,” perfectly describing how these tires function.
Understanding pneumatic tires requires recognizing their unique ability to maintain shape and structure through internal air pressure. Unlike their solid counterparts, these tires provide a perfect balance of rigidity and flexibility, making them ideal for various applications. The compressed air chamber within the tire creates a dynamic system that responds to road conditions, offering superior performance in diverse situations.
The innovation behind pneumatic tires lies in their ability to distribute weight evenly across the contact patch – the area where the tire meets the road. This distribution helps create optimal traction while minimizing wear, making them more efficient and durable than other tire types. The technology continues to evolve, incorporating new materials and design principles to enhance performance further. As research and development in tire engineering progress, pneumatic tires are set to become even more advanced, offering improved safety features, increased fuel efficiency, and better environmental sustainability.
How does a pneumatic tire differ from other types of tires?
Pneumatic tires stand apart from other tire varieties through their unique construction and operational principles. The most distinctive feature is their use of pressurized air as a core component, which creates a flexible, responsive system that adapts to various road conditions. This adaptability makes them significantly more versatile than alternative tire types, offering superior performance across different terrains and weather conditions.
The fundamental difference lies in how pneumatic tires handle impact and distribute weight. When encountering obstacles or uneven surfaces, the compressed air within the tire compresses and expands, creating a natural shock absorption system. This dynamic response mechanism is something that solid rubber tires cannot replicate, making pneumatic tires the preferred choice for most modern vehicles.
Modern pneumatic tire design incorporates advanced technologies that maximize grip and handling capabilities. The Tire and Rubber Association of Canada reports that continuous improvements in tire compound development and tread design have significantly enhanced traction performance across various weather conditions and road surfaces. These advancements not only improve vehicle safety but also contribute to increased fuel efficiency and reduced environmental impact.
Pneumatic tires vs solid tires
The comparison between pneumatic and solid tires reveals significant differences in performance, comfort, and application suitability. Solid tires, while virtually maintenance-free and puncture-proof, lack the sophisticated shock absorption and adaptability that make pneumatic tires superior for most applications. Here’s a detailed comparison of their characteristics:
Feature | Pneumatic Tires | Solid Tires |
---|---|---|
Shock Absorption | Excellent | Poor |
Maintenance Requirements | Regular monitoring needed | Minimal |
Weight | Lighter | Heavier |
Ride Comfort | Superior | Limited |
Puncture Risk | Yes | No |
Heat Dissipation | Efficient | Less efficient |
Cost | Generally higher | Generally lower |
Traction | Excellent | Good |
The comparison highlights why pneumatic tires dominate the automotive industry despite requiring more maintenance. Their superior performance characteristics make them the ideal choice for vehicles that need to maintain high levels of comfort and safety while operating at various speeds and conditions. The National Highway Traffic Safety Administration provides extensive research supporting these performance differences and emphasizes the importance of proper tire maintenance for vehicle safety.
Pneumatic tires vs semi-pneumatic tires
Semi-pneumatic tires occupy a middle ground between fully pneumatic and solid tires, offering some unique advantages and limitations. These tires feature a solid inner core surrounded by air pockets, creating a hybrid solution that aims to combine the best aspects of both designs. Let’s examine their comparative features:
Characteristic | Pneumatic Tires | Semi-Pneumatic Tires |
---|---|---|
Air Pressure | Requires monitoring | No monitoring needed |
Shock Absorption | Highest | Moderate |
Durability | Moderate | High |
Load Capacity | Variable | Fixed |
Cost Efficiency | Moderate | High |
Maintenance | Regular | Minimal |
Performance | Superior | Good |
Versatility | Highest | Limited |
The distinction between these tire types becomes particularly important in specialized applications. According to Tire Industry Research, understanding these differences is crucial for selecting the right tire type for specific vehicles and use cases. While semi-pneumatic tires offer advantages in terms of durability and cost-efficiency, they may not provide the same level of performance and versatility as fully pneumatic tires in most general applications.
Pneumatic tires vs cushion tires
Cushion tires present another alternative in the tire market, particularly in industrial applications where specific operating conditions demand unique tire characteristics. These tires offer distinct advantages in certain scenarios while having limitations that make them less suitable for general use compared to pneumatic tires.
The primary differences become apparent when examining their structural characteristics and performance attributes:
Aspect | Pneumatic Tires | Cushion Tires |
---|---|---|
Construction | Air-filled | Solid rubber |
Comfort Level | High | Moderate |
Installation | Complex | Simple |
Load Bearing | Adjustable | Fixed |
Operating Speed | Higher | Lower |
Surface Adaptation | Excellent | Limited |
Initial Cost | Higher | Lower |
Lifespan | Variable | Extended |
Research from Tire Industry Research indicates that while cushion tires excel in specific industrial applications, pneumatic tires remain superior for general transportation needs due to their versatility and performance characteristics. The choice between these tire types depends heavily on the specific requirements of the application, such as load capacity, operating speed, and surface conditions.
Are pneumatic tires tubeless or do they have inner tubes?
Modern pneumatic tires come in both tubeless and tube-type configurations, each designed for specific applications and vehicle types. The evolution of tire technology has led to significant improvements in both designs, though tubeless tires have become increasingly prevalent in contemporary vehicles. Understanding the differences between these two types helps in making informed decisions about tire selection and maintenance.
The development of tubeless tire technology represents one of the most significant advancements in tire design, as noted by the European Tyre and Rubber Manufacturers’ Association. This innovation has dramatically improved safety and reliability while reducing maintenance requirements. According to industry experts at Bridgestone, tubeless tires offer enhanced stability and better heat dissipation compared to their tube-type counterparts.
The choice between tubeless and tube-type tires often depends on specific vehicle requirements and operating conditions. Here’s a comprehensive comparison of both types:
Design Element | Tubeless Tires | Tube-Type Tires |
---|---|---|
Air Retention | Superior | Good |
Heat Generation | Lower | Higher |
Puncture Safety | Better | Fair |
Installation | Complex | Simple |
Maintenance | Less frequent | More frequent |
Cost | Higher initial | Lower initial |
Weight | Lighter | Heavier |
Rim Requirements | Special design | Standard |
While tubeless tires have become the preferred choice for most modern vehicles due to their superior performance and safety features, tube-type tires still find applications in certain vehicle types and markets. According to the Tire and Rim Association, the selection between these two tire types should be based on factors such as vehicle design, intended use, and maintenance capabilities. Proper installation and maintenance practices are crucial for ensuring optimal performance and safety, regardless of the tire type chosen.
What are the Key Components of a Pneumatic Tire?
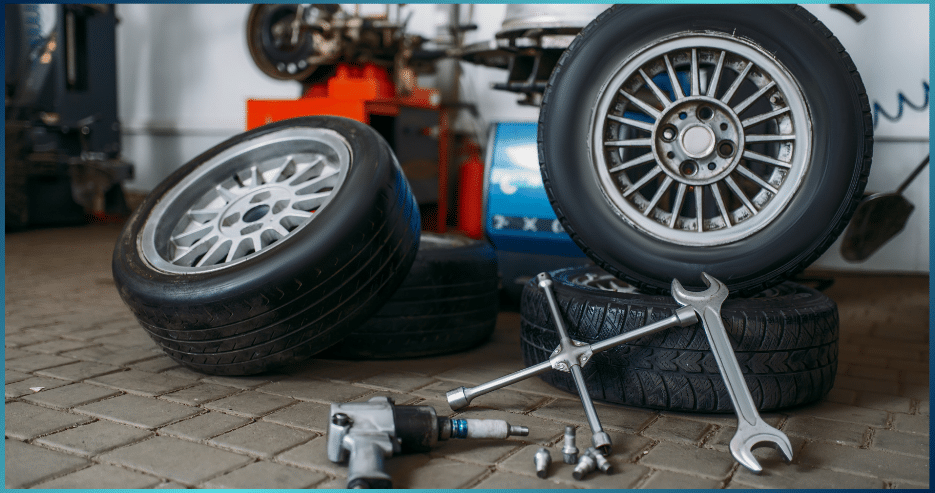
Understanding the complex structure of pneumatic tires requires examining their various components and how they work together. The modern pneumatic tire represents decades of engineering refinement, combining multiple layers of specialized materials to create a reliable and efficient transportation solution. According to the Tire and Rim Association, each component plays a crucial role in the tire’s overall performance and safety.
The intricate design of pneumatic tires involves several key elements working in harmony to provide optimal performance. These components must withstand extreme conditions while maintaining their structural integrity. The Rubber Manufacturers Association emphasizes that understanding these components is essential for proper tire maintenance and safety.
Research from Michelin’s Technology Center shows that modern pneumatic tires contain more than 200 different raw materials, all carefully selected and engineered to perform specific functions. This complex composition ensures that tires can meet the demanding requirements of modern vehicles while providing superior safety and comfort. As tire technology continues to advance, new materials and construction methods are being developed to further enhance tire performance, durability, and environmental sustainability.
What materials are pneumatic tires made from?
The construction of pneumatic tires involves a sophisticated blend of natural and synthetic materials, each chosen for its specific properties and contributions to overall tire performance. Here’s a detailed breakdown of the primary materials used in modern pneumatic tires:
Material Type | Primary Function | Characteristics |
---|---|---|
Natural Rubber | Base structure | High elasticity, durability |
Synthetic Rubber | Performance enhancement | Weather resistance, grip |
Steel | Reinforcement | Structural strength |
Polyester | Cord material | Dimensional stability |
Carbon Black | Reinforcement | UV protection, wear resistance |
Silica | Grip enhancement | Wet traction, rolling resistance |
Antioxidants | Protection | Age resistance |
Plasticizers | Flexibility | Temperature adaptation |
According to the International Rubber Study Group, the precise combination of these materials significantly influences tire performance characteristics. The manufacturing process requires careful control of numerous variables to ensure consistent quality and reliability. Advancements in material science and manufacturing techniques have led to the development of more sustainable and eco-friendly tire components, such as the use of renewable resources and recycled materials, as reported by the Rubber Manufacturers Association.
How is a pneumatic tire constructed?
The construction process of pneumatic tires involves multiple stages and precise engineering to create a product that can withstand diverse operating conditions. Modern tire manufacturing combines advanced automation with skilled craftsmanship to produce tires that meet rigorous safety and performance standards.
Key construction phases include:
- Component Preparation: Processing raw materials into usable forms
- Layer Assembly: Building up the tire structure layer by layer
- Vulcanization: Heat-treating to create the final product
- Quality Control: Testing for uniformity and performance
- Final Inspection: Verifying compliance with safety standards
The Continental Tire Technical Center provides extensive research on how these construction phases contribute to tire performance and longevity. Innovations in manufacturing processes, such as the use of 3D modeling and simulation, have enabled tire manufacturers to optimize tire design and construction for specific applications and operating conditions.
Tread
The tread design of pneumatic tires represents one of the most critical aspects of tire engineering. This outer layer directly contacts the road surface and must provide optimal traction under various conditions. According to Goodyear’s Research Division, tread patterns are carefully designed to:
Tread Feature | Purpose | Benefits |
---|---|---|
Grooves | Water evacuation | Hydroplaning resistance |
Sipes | Edge creation | Winter traction |
Blocks | Surface contact | Dry handling |
Shoulder design | Cornering stability | Improved handling |
Wear indicators | Maintenance monitoring | Safety monitoring |
Noise reduction | Comfort enhancement | Quieter operation |
Advancements in tread design have led to the development of specialized tread patterns for different driving conditions, such as all-season, winter, and performance tires. These designs optimize tire performance and safety by adapting to specific road conditions and vehicle requirements.
Sidewall
The sidewall serves as a crucial component in pneumatic tire design, providing structural support while allowing necessary flexion during operation. This section of the tire must balance multiple requirements:
Sidewall Aspect | Function | Performance Impact |
---|---|---|
Thickness | Load support | Durability |
Flexibility | Ride comfort | Handling response |
Protection | Damage resistance | Longevity |
Markings | Information display | Safety compliance |
UV resistance | Environmental protection | Aging prevention |
Heat dissipation | Temperature control | Performance stability |
The sidewall design must also incorporate essential information about the tire, such as size, load capacity, speed rating, and manufacturing details, as required by regulatory agencies like the National Highway Traffic Safety Administration.
Bead
The bead represents a critical safety component in pneumatic tire design, ensuring secure mounting to the wheel rim. This often-overlooked element plays a vital role in tire performance and safety:
Bead Component | Purpose | Safety Contribution |
---|---|---|
Steel wire | Structural strength | Mounting security |
Rubber coating | Rim protection | Air sealing |
Shape design | Fit optimization | Installation ease |
Wire bundle | Load capacity | Stability |
Apex rubber | Sidewall support | Handling precision |
The bead design must provide a strong, airtight seal between the tire and the wheel rim to maintain proper inflation pressure and prevent the tire from slipping or detaching during operation. Advancements in bead design, such as the use of high-strength steel wires and optimized rubber compounds, have further enhanced tire safety and performance.
What is the role of air pressure in pneumatic tires?
Air pressure serves as the fundamental operating principle of pneumatic tires, playing a critical role in their performance, safety, and longevity. The precise management of air pressure within these tires directly influences various aspects of vehicle operation, from fuel efficiency to handling characteristics. According to the National Highway Traffic Safety Administration, maintaining proper tire pressure is one of the most important aspects of vehicle maintenance.
Understanding how air pressure affects tire performance requires considering multiple factors that work together. The Tire Industry Research has conducted extensive studies showing that even small variations in tire pressure can significantly impact vehicle safety and performance. Their research demonstrates that proper tire inflation contributes to optimal tire footprint, load distribution, and overall vehicle stability.
Modern tire pressure monitoring systems (TPMS) have revolutionized how we manage tire pressure. The European Tyre and Rubber Manufacturers’ Association reports that these systems have significantly improved road safety by helping drivers maintain optimal tire pressure. Here’s a detailed look at how different pressure levels affect tire performance:
Pressure Level | Impact on Performance | Safety Implications |
---|---|---|
Optimal | Best handling and efficiency | Maximum safety |
Under-inflated | Increased wear and fuel consumption | Reduced stability |
Over-inflated | Reduced traction and comfort | Compromised handling |
Severely under-inflated | Risk of tire failure | Dangerous conditions |
Variable pressure | Uneven wear patterns | Unpredictable handling |
Maintaining proper tire pressure not only enhances vehicle safety and performance but also contributes to improved fuel efficiency and longer tire life. Regular tire pressure checks and adjustments should be an integral part of any vehicle maintenance routine, as recommended by the Tire Industry Association.
Who Invented the Pneumatic Tire and When?
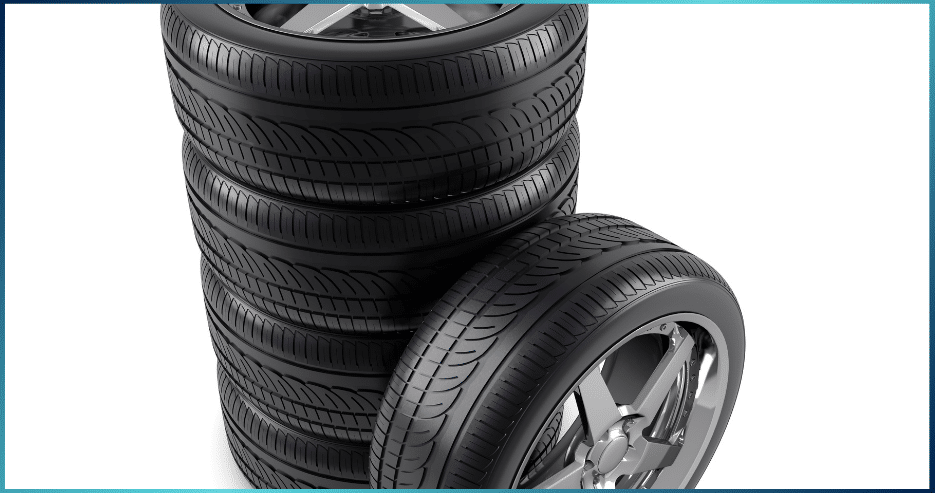
The invention of the pneumatic tire marks a pivotal moment in transportation history. John Boyd Dunlop, a Scottish veterinarian, is credited with creating the first practical pneumatic tire in 1888. His invention, initially designed for his son’s tricycle, would revolutionize transportation and lay the foundation for modern tire technology.
The journey from Dunlop’s initial prototype to today’s sophisticated tire designs involved numerous innovations and improvements. The Dunlop Archive provides fascinating insights into the early development stages and subsequent improvements that shaped modern tire technology. These early advancements focused on improving tire durability, traction, and overall performance, paving the way for the widespread adoption of pneumatic tires in the automotive industry.
Research from the Smithsonian Institution reveals that several inventors contributed to pneumatic tire development before and after Dunlop’s breakthrough. These collaborative efforts over decades helped create the highly engineered products we use today. The collective work of inventors, engineers, and tire manufacturers has led to a continuous evolution of pneumatic tire technology, addressing the ever-changing needs of transportation and ensuring safer, more efficient travel.
What problem was the pneumatic tire invented to solve?
The primary motivation behind the invention of pneumatic tires was to address several significant challenges faced by early transportation methods:
- Ride Comfort: Solid wheels created uncomfortable vibrations
- Vehicle Damage: Excessive shock transmission damaged vehicle components
- Operator Fatigue: Constant vibration caused driver exhaustion
- Speed Limitations: Solid wheels restricted maximum safe speeds
- Surface Impact: Hard wheels damaged road surfaces
- Load Distribution: Weight concentration caused excessive wear
The Science Museum Group documents how these early challenges drove innovation in tire design and construction methods. The development of pneumatic tires sought to mitigate these issues by providing a cushioning effect, absorbing shocks, and distributing weight more evenly. This led to improved ride comfort, reduced vehicle damage, and increased operational efficiency.
How has the pneumatic tire design evolved over time?
The evolution of pneumatic tire design represents a fascinating journey of technological advancement and innovation. From simple rubber tubes to today’s sophisticated compounds and construction methods, tire development has continuously adapted to meet changing transportation needs.
Key evolutionary milestones include:
Time Period | Innovation | Impact on Industry |
---|---|---|
1888-1900 | Basic pneumatic design | Improved comfort |
1900-1920 | Cord reinforcement | Enhanced durability |
1920-1940 | Balloon tires | Better load capacity |
1940-1960 | Radial construction | Revolutionary performance |
1960-1980 | Steel-belted radials | Increased longevity |
1980-2000 | All-season compounds | Versatile performance |
2000-Present | Smart tire technology | Enhanced safety |
The Tire Industry Project provides comprehensive research on how tire design has evolved to meet modern challenges while improving safety and performance. Each evolutionary stage has addressed specific needs, from improving ride comfort in the early days to enhancing safety and performance in modern times. Today, advancements in materials science, manufacturing processes, and digital technologies continue to drive innovation in pneumatic tire design, focusing on sustainability, efficiency, and connectivity.
What are the Benefits and Advantages of Using Pneumatic Tires?
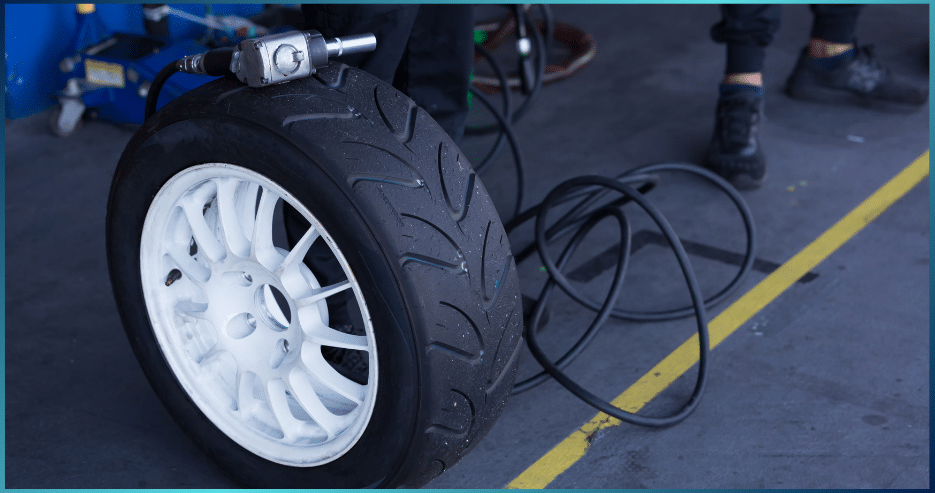
Pneumatic tires offer numerous advantages that have made them the standard choice for most vehicles today. Their unique design principles provide a combination of performance characteristics that significantly enhance vehicle operation and safety. According to the Transportation Research Board, pneumatic tires have revolutionized modern transportation through their superior performance capabilities.
The widespread adoption of pneumatic tires across various industries demonstrates their versatility and effectiveness. The European Automobile Manufacturers Association reports that these tires have become integral to achieving optimal vehicle performance, fuel efficiency, and safety standards in modern vehicles. The ability of pneumatic tires to adapt to different driving conditions and provide a comfortable, stable ride has made them indispensable for both personal and commercial transportation.
Research conducted by the Japan Automobile Manufacturers Association shows that pneumatic tires contribute significantly to vehicle handling, stability, and overall safety performance. Their studies highlight how these tires have evolved to meet increasingly demanding performance requirements, incorporating advanced technologies such as run-flat designs and self-sealing capabilities. The continuous improvement of pneumatic tire technology has been driven by the need to enhance vehicle safety, reduce environmental impact, and improve overall operational efficiency.
How do pneumatic tires provide a smoother ride compared to solid tires?
The superior ride quality of pneumatic tires stems from their unique ability to absorb and dissipate road impacts effectively. This characteristic is particularly important for both passenger comfort and vehicle longevity. Let’s examine the key factors that contribute to their smooth ride characteristics:
Ride Quality Factor | Pneumatic Tire Performance | Impact on Experience |
---|---|---|
Shock Absorption | Excellent impact dampening | Reduced vibration |
Surface Adaptation | Continuous road contact | Improved stability |
Load Distribution | Even weight spreading | Better balance |
Resonance Control | Minimized frequency transfer | Lower noise levels |
Flexibility | Dynamic response | Enhanced comfort |
Energy Dissipation | Efficient impact absorption | Reduced fatigue |
The ability of pneumatic tires to absorb shocks and vibrations is primarily due to the compressibility of the air within the tire. As the tire encounters road irregularities, the air compresses and expands, acting as a natural cushioning system. This process helps to isolate the vehicle and its occupants from the effects of rough road surfaces, resulting in a smoother, more comfortable ride. In contrast, solid tires lack this adaptive cushioning effect, transmitting more vibrations and shocks to the vehicle and its passengers.
Why are pneumatic tires more efficient than solid tires?
The efficiency advantages of pneumatic tires extend beyond basic performance metrics to include significant operational benefits. These advantages have made them the preferred choice for most vehicle applications:
- Reduced Energy Loss: Better conversion of power to motion
- Lower Operating Temperatures: More efficient heat dissipation
- Optimized Contact Patch: Improved ground interaction
- Dynamic Load Response: Better adaptation to changing conditions
- Enhanced Grip Characteristics: Superior traction in various conditions
- Reduced Vehicle Wear: Lower transmission of road impacts
The Institute of Transport Studies has conducted extensive research demonstrating these efficiency benefits. Their studies show that pneumatic tires contribute to improved fuel economy, reduced tire wear, and lower overall vehicle maintenance costs compared to solid tires. The ability of pneumatic tires to maintain optimal contact with the road surface and respond dynamically to changing loads and conditions is key to their enhanced efficiency.
Lower rolling resistance
Rolling resistance plays a crucial role in vehicle efficiency and energy consumption. Pneumatic tires have been engineered to minimize this resistance while maintaining optimal performance characteristics:
Resistance Factor | Impact on Efficiency | Energy Savings |
---|---|---|
Tread Design | Optimized ground contact | 2-5% fuel savings |
Inflation Pressure | Reduced deformation | 3-7% efficiency gain |
Compound Technology | Lower heat generation | 4-8% energy conservation |
Structure Design | Minimal energy loss | 2-4% improved efficiency |
Temperature Management | Optimal operating range | 1-3% better performance |
Lower rolling resistance in pneumatic tires is achieved through a combination of factors, including advanced tread designs, optimized inflation pressure, and the use of specialized rubber compounds. These features work together to minimize energy loss as the tire rolls, reducing fuel consumption and improving overall vehicle efficiency. Solid tires, lacking these design optimizations, typically have higher rolling resistance, leading to increased energy consumption and reduced efficiency.
Fuel efficiency
The relationship between pneumatic tires and fuel efficiency has become increasingly important in modern vehicle design. According to the International Energy Agency, tire design can significantly impact overall vehicle fuel consumption:
- Proper Inflation: Maintains optimal rolling resistance
- Advanced Compounds: Reduces energy loss
- Tread Patterns: Minimizes unnecessary friction
- Structural Design: Optimizes energy transfer
- Weight Reduction: Decreases rotational mass
- Temperature Management: Maintains efficient operation
Pneumatic tires contribute to improved fuel efficiency by reducing energy losses and optimizing the tire’s interaction with the road surface. Maintaining proper tire inflation, using advanced rubber compounds, and optimizing tread patterns all help to minimize rolling resistance and improve fuel economy. In contrast, solid tires, with their higher rolling resistance and less efficient design, can negatively impact fuel consumption, leading to increased operating costs and environmental impact.
What are the load-bearing and weight distribution advantages of pneumatic tires?
The load-bearing capabilities of pneumatic tires represent one of their most significant advantages over other tire types. Their design allows for optimal weight distribution while maintaining performance characteristics:
Load Aspect | Advantage | Performance Benefit |
---|---|---|
Weight Distribution | Even pressure spread | Reduced road damage |
Load Flexibility | Adjustable capacity | Versatile usage |
Impact Absorption | Dynamic response | Protected cargo |
Structural Support | Maintained stability | Safer operation |
Contact Management | Optimized footprint | Better traction |
Pneumatic tires excel in load-bearing and weight distribution due to their ability to evenly spread the vehicle’s weight across the tire’s contact patch. The air pressure within the tire helps to distribute the load uniformly, reducing stress concentrations and minimizing road surface damage. Additionally, pneumatic tires offer flexibility in load capacity, as the air pressure can be adjusted to accommodate different load requirements. This adaptability makes pneumatic tires suitable for a wide range of applications, from lightweight passenger vehicles to heavy-duty commercial trucks.
How do pneumatic tires offer better traction and handling?
The superior traction and handling capabilities of pneumatic tires stem from their unique design characteristics and material properties. According to the Society of Automotive Engineers, the interaction between pneumatic tires and road surfaces creates optimal conditions for vehicle control and stability. This complex relationship involves multiple factors working together to enhance overall performance.
Modern pneumatic tire design incorporates advanced technologies that maximize grip and handling capabilities. The Tire Industry Association reports that continuous improvements in tire compound development and tread design have significantly enhanced traction performance across various weather conditions and road surfaces. These advancements have led to the development of specialized tire categories, such as high-performance tires, all-terrain tires, and winter tires, each designed to provide optimal traction and handling in specific driving conditions.
Research conducted by Continental’s Testing Facility demonstrates how pneumatic tires achieve superior traction through their ability to maintain consistent contact with the road surface. Here’s a detailed analysis of key traction and handling characteristics:
Performance Aspect | Feature | Benefit |
---|---|---|
Surface Contact | Adaptive footprint | Enhanced grip |
Cornering Stability | Sidewall flexibility | Better control |
Wet Performance | Groove design | Water evacuation |
Dry Handling | Compound technology | Precise response |
Emergency Maneuvers | Structure integrity | Quick recovery |
Temperature Range | Material optimization | Consistent performance |
The traction and handling advantages of pneumatic tires are further enhanced by advanced technologies such as directional tread patterns, asymmetric designs, and self-supporting run-flat constructions. These innovations contribute to improved steering response, cornering stability, and overall vehicle control, even in challenging driving conditions. In comparison, solid tires, with their rigid construction and limited adaptability, often struggle to provide the same level of traction and handling performance across a wide range of surfaces and weather conditions.
What are the Common Applications and Uses for Pneumatic Tires?
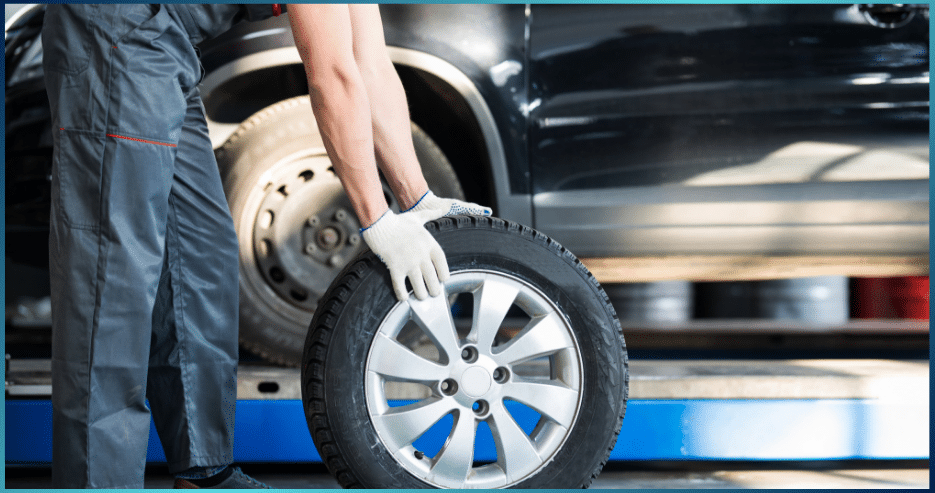
The versatility of pneumatic tires has led to their adoption across numerous industries and applications. These tires have become essential components in various modes of transportation and equipment, each designed to meet specific operational requirements.
Which vehicles commonly use pneumatic tires?
Different vehicles require specific tire characteristics to perform optimally. Here’s a comprehensive overview of common vehicle applications:
Cars and trucks
The automotive sector represents the largest application for pneumatic tires, with specific designs for various vehicle types:
Vehicle Category | Tire Requirements | Performance Focus |
---|---|---|
Passenger Cars | Comfort and efficiency | Daily commuting |
SUVs | Versatility | Mixed-use capability |
Light Trucks | Load capacity | Commercial use |
Heavy Trucks | Durability | Long-haul transport |
Performance Vehicles | High-speed stability | Sport handling |
Pneumatic tires for cars and trucks are engineered to meet the specific demands of each vehicle category, balancing factors such as ride comfort, fuel efficiency, load capacity, and performance. Advancements in tire technology, such as the development of low rolling resistance compounds and noise-reducing tread patterns, have further enhanced the suitability of pneumatic tires for automotive applications.
Bicycles and motorcycles
Two-wheeled vehicles present unique challenges for pneumatic tire design:
- Racing Bicycles: High-pressure, low-rolling resistance
- Mountain Bikes: Enhanced grip and durability
- Sport Motorcycles: Extreme grip and stability
- Touring Motorcycles: Long-distance comfort
- Urban Scooters: All-weather reliability
The International Motorcycle Manufacturers Association provides detailed specifications for various two-wheeler applications. Pneumatic tires for bicycles and motorcycles are designed to provide optimal performance, handling, and safety for each specific use case. Advanced technologies, such as tubeless tire systems and puncture-resistant compounds, have further enhanced the capabilities of pneumatic tires in these applications.
Forklifts
Industrial applications like forklifts require specialized pneumatic tire designs:
Application Type | Tire Characteristic | Operational Benefit |
---|---|---|
Indoor Use | Non-marking compounds | Floor protection |
Outdoor Operation | All-terrain capability | Versatility |
Heavy Lifting | High load capacity | Safety margin |
Extended Use | Wear resistance | Longevity |
Rough Surfaces | Impact protection | Equipment safety |
Pneumatic tires for forklifts are engineered to withstand the unique demands of industrial environments, such as heavy loads, rough surfaces, and extended operating hours. Special compounds and tread designs are used to provide optimal traction, stability, and wear resistance, ensuring safe and efficient material handling operations.
Lawnmowers
Lawn and garden equipment benefits from specific pneumatic tire designs:
- Residential Mowers: Turf protection features
- Commercial Units: Extended service life
- Zero-Turn Models: Enhanced maneuverability
- Riding Mowers: Comfort optimization
- Push Mowers: Easy rolling characteristics
Pneumatic tires for lawnmowers are designed to provide a balance of traction, maneuverability, and turf protection. Different tread patterns and rubber compounds are used to suit the specific requirements of each type of mower, from lightweight push models to heavy-duty commercial units. These specialized tires help to ensure efficient and effective lawn maintenance while minimizing damage to the turf.
What are pneumatic tires used for in industrial and construction settings?
Industrial and construction environments demand exceptional performance from pneumatic tires. These specialized applications require tires that can withstand extreme conditions while maintaining safety and efficiency. The Construction Equipment Association emphasizes the critical role of proper tire selection in maximizing equipment productivity and safety.
Modern construction sites present unique challenges that influence tire design requirements. According to the Association of Equipment Manufacturers, pneumatic tires must balance durability with performance to meet the demanding conditions of construction environments. Their research shows that proper tire selection can significantly impact project efficiency and equipment longevity.
The European Construction Industry Federation provides comprehensive guidelines for selecting appropriate pneumatic tires based on specific construction applications. These recommendations help optimize equipment performance while ensuring safe operation. The use of specialized tire constructions, such as steel-belted radials and puncture-resistant compounds, has greatly enhanced the capabilities of pneumatic tires in industrial and construction settings.
Earthmoving equipment
Earthmoving operations require specialized tire characteristics to maintain efficiency and safety:
Equipment Type | Tire Requirements | Operating Conditions |
---|---|---|
Bulldozers | Cut resistance | Rocky terrain |
Excavators | Stability | Uneven surfaces |
Loaders | Load capacity | Variable loads |
Graders | Precision control | Grade work |
Scrapers | Wear resistance | Abrasive conditions |
Pneumatic tires for earthmoving equipment are designed to provide exceptional traction, stability, and durability in challenging off-road conditions. These tires feature aggressive tread patterns, reinforced sidewalls, and specialized rubber compounds to withstand the rigors of heavy-duty construction work. The use of advanced tire technologies, such as self-cleaning treads and cut-resistant casings, further enhances the performance and longevity of pneumatic tires in earthmoving applications.
Cranes
Crane operations demand specific tire characteristics to ensure safe and efficient lifting:
- Static Stability: Essential for precise positioning
- Load Distribution: Critical for operational safety
- Surface Protection: Minimizes ground damage
- Maneuverability: Enables precise movements
- Weather Resistance: Maintains performance in various conditions
Pneumatic tires for cranes are engineered to provide maximum stability and load support, even when operating on uneven surfaces or in challenging weather conditions. The use of high-load-capacity tire constructions and specialized tread designs helps to ensure safe and efficient crane operations, minimizing the risk of accidents and equipment damage.
How are pneumatic tires utilized on mobility devices?
The application of pneumatic tires in mobility devices represents a critical advancement in assistive technology. The American Association of People with Disabilities highlights how proper tire selection can significantly impact user comfort and independence. Pneumatic tires for mobility devices are designed to provide a smooth, stable ride while minimizing the effort required for propulsion and maneuvering.
Wheelchairs
Wheelchair tire design focuses on user comfort and mobility:
Wheelchair Type | Tire Feature | User Benefit |
---|---|---|
Manual | Light weight | Easy propulsion |
Power | Durability | Extended service |
Sport | High performance | Enhanced control |
All-terrain | Versatility | Outdoor capability |
Transport | Stability | Safe operation |
Pneumatic tires for wheelchairs are engineered to meet the specific needs of each wheelchair type, balancing factors such as weight, durability, and performance. The use of lightweight materials and optimized tread patterns helps to reduce rolling resistance, making it easier for users to propel manual wheelchairs. For power wheelchairs, pneumatic tires provide a smooth, stable ride, enhancing user comfort and safety.
Walkers and rollators
Mobility aid tires require specific design considerations:
- Smooth Rolling: Reduces user effort
- Stability: Enhances safety
- Durability: Minimizes maintenance
- Grip: Ensures reliable traction
- Comfort: Reduces vibration transmission
Pneumatic tires for walkers and rollators are designed to provide a stable, comfortable experience for users, even when navigating uneven surfaces or outdoor environments. The use of specialized rubber compounds and tread patterns helps to ensure reliable traction and smooth rolling, reducing the risk of slips and falls. Additionally, the shock-absorbing properties of pneumatic tires help to minimize vibration transmission, enhancing user comfort and reducing fatigue.
What are some specialty applications of pneumatic tires?
Specialty applications demonstrate the versatility of pneumatic tire technology in meeting unique operational requirements. The Aerospace Industries Association provides extensive documentation on specialized tire applications, highlighting the critical role of pneumatic tires in ensuring safe and efficient operations in demanding environments.
Aircraft landing gear
Aircraft tires represent the pinnacle of pneumatic tire engineering:
Application | Critical Features | Performance Requirements |
---|---|---|
Commercial | High speed rating | Safe landings |
Military | Extreme durability | Combat readiness |
Private | Weight efficiency | Operational flexibility |
Cargo | Load capacity | Heavy transport |
Training | Cost efficiency | Frequent use |
Pneumatic tires for aircraft landing gear are designed to withstand the extreme forces and temperatures associated with high-speed landings and takeoffs. These tires feature advanced materials, such as high-strength steel belts and heat-resistant rubber compounds, to ensure maximum safety and performance. The use of specialized tread patterns and reinforced sidewalls helps to minimize the risk of tire failure, even under the most demanding operating conditions.
Racing cars
Professional racing demands the ultimate in tire performance:
- Maximum Grip: Optimal track performance
- Temperature Management: Consistent handling
- Rapid Response: Precise control
- Wear Characteristics: Strategic pit stops
- Safety Features: High-speed stability
Pneumatic tires for racing cars are engineered to provide the highest levels of grip, handling, and performance, allowing drivers to push their vehicles to the limits. The use of advanced rubber compounds, specialized tread patterns, and lightweight construction helps to maximize tire performance, while also ensuring driver safety. Racing tires are designed to operate within specific temperature ranges, providing consistent handling characteristics throughout the duration of a race.
These specialized applications showcase the adaptability of pneumatic tire technology in meeting diverse operational requirements while maintaining safety and performance standards. The continuous development of new materials, construction methods, and design innovations ensures that pneumatic tires will continue to evolve, meeting the ever-changing demands of specialty applications.
What are the Different Types and Sizes of Pneumatic Tires?
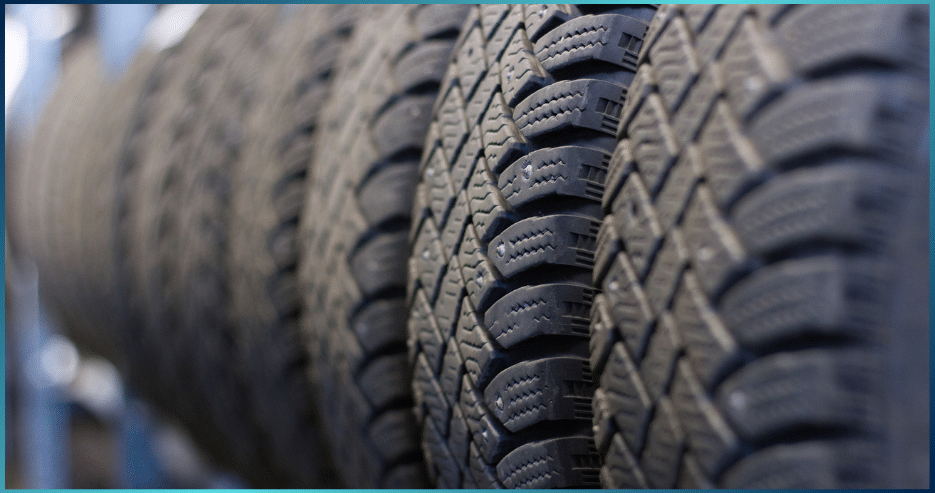
The diversity of pneumatic tire types and sizes reflects the wide range of applications they serve. According to the European Tyre and Rim Technical Organisation, standardization of tire sizes and types has been crucial for ensuring compatibility and safety across different vehicles and applications. Understanding these variations helps in selecting the most appropriate tire for specific needs.
The International Organization for Standardization has established comprehensive guidelines for tire sizing and classification, ensuring global consistency in tire specifications. These standards help manufacturers and users make informed decisions about tire selection and application. Adhering to these standards is essential for maintaining vehicle safety, performance, and efficiency.
Research from the World Tire Manufacturing Association shows that proper tire size selection significantly impacts vehicle performance, safety, and efficiency. Their studies emphasize the importance of understanding tire sizing conventions and applications. Selecting the correct tire size ensures optimal vehicle handling, stability, and fuel economy while also promoting even tire wear and extending tire life.
What are the most common pneumatic tire sizes?
Different applications require specific tire sizes to optimize performance and safety. Here’s a detailed examination of common tire sizes and their applications:
10 inch pneumatic tires
Ten-inch pneumatic tires serve various specialized applications:
Application | Load Rating | Speed Rating | Typical Use |
---|---|---|---|
Hand Trucks | 300-600 lbs | Low speed | Material handling |
Golf Carts | 800-1200 lbs | Medium speed | Recreational |
Utility Trailers | 1000-1500 lbs | Highway speed | Light transport |
Garden Equipment | 400-800 lbs | Variable | Outdoor maintenance |
Mobility Devices | 250-500 lbs | Low speed | Personal mobility |
Ten-inch pneumatic tires are designed to provide a balance of load capacity, speed rating, and durability for their specific applications. The use of specialized rubber compounds and tread patterns helps to ensure optimal performance and safety, whether the tires are used for material handling, recreational vehicles, or personal mobility devices.
13 inch pneumatic tires
Thirteen-inch tires commonly appear in specific vehicle categories:
- Compact Cars: Efficient urban transportation
- Light Trailers: Recreational and utility use
- Small Commercial: Delivery vehicles
- Classic Vehicles: Vintage automobiles
- Performance Applications: Specialized racing
Thirteen-inch pneumatic tires are engineered to provide a combination of fuel efficiency, handling, and durability for smaller vehicles and specialized applications. The use of advanced rubber compounds and optimized tread patterns helps to maximize tire performance while also ensuring a smooth, comfortable ride.
8 inch pneumatic tires
Eight-inch tires find applications in numerous specialized uses:
Equipment Type | Primary Use | Performance Requirements |
---|---|---|
Wheelchairs | Daily mobility | Comfort and durability |
Dollies | Material handling | Load capacity |
Carts | Light transport | Maneuverability |
Small Equipment | Various | Versatility |
Children’s Vehicles | Recreational | Safety |
Eight-inch pneumatic tires are designed to provide reliable performance and durability for a wide range of specialized applications. The use of lightweight materials and optimized tread patterns helps to ensure easy maneuverability and a smooth ride, while also providing the necessary load capacity and stability for safe operation.
What are the differences between bias-ply and radial pneumatic tires?
The distinction between bias-ply and radial tire construction represents a fundamental choice in tire technology:
Feature | Bias-Ply | Radial |
---|---|---|
Construction | Crisscross layers | Perpendicular plies |
Flexibility | Limited | Superior |
Heat Generation | Higher | Lower |
Cost | Less expensive | More expensive |
Durability | Good | Excellent |
Performance | Basic | Advanced |
Applications | Traditional | Modern |
Radial tires have largely replaced bias-ply tires in most modern applications due to their superior performance characteristics. The use of perpendicular plies in radial tire construction provides increased flexibility, lower heat generation, and improved durability compared to the crisscross layer design of bias-ply tires. Radial tires also offer advanced performance capabilities, such as enhanced handling and reduced rolling resistance, making them the preferred choice for most contemporary vehicles.
How do you choose the right pneumatic tire for your application?
Selecting the appropriate pneumatic tire involves considering multiple factors:
- Load Requirements: Weight capacity needs
- Speed Ratings: Maximum operational speed
- Environmental Conditions: Operating surface and weather
- Maintenance Capabilities: Service requirements
- Cost Considerations: Budget constraints
- Performance Needs: Handling and efficiency requirements
The Tire and Rubber Association provides comprehensive guidelines for tire selection based on specific applications and requirements:
Selection Factor | Consideration Points | Impact on Choice |
---|---|---|
Vehicle Type | Design specifications | Compatibility |
Usage Pattern | Duty cycle | Durability needs |
Climate | Weather conditions | Compound selection |
Terrain | Surface conditions | Tread pattern |
Budget | Life cycle cost | Value assessment |
Safety Requirements | Performance ratings | Risk management |
Choosing the right pneumatic tire requires careful consideration of the specific application, operating conditions, and performance requirements. Factors such as vehicle type, usage patterns, and environmental conditions play a critical role in determining the most suitable tire for a given situation. Additionally, budget constraints and safety requirements must be considered to ensure the selected tire provides the best value and performance while minimizing risk. Consulting with tire professionals and referring to manufacturer guidelines can help in making an informed decision.
What are Some Potential Issues with Pneumatic Tires and How Can They Be Addressed?
Managing potential issues with pneumatic tires requires understanding common problems and their solutions. The National Transportation Safety Board emphasizes that proper tire maintenance and awareness of potential issues are crucial for vehicle safety and performance. Regular monitoring and preventive maintenance can help avoid many common tire-related problems.
Research from the Tire Industry Safety Council indicates that most tire issues can be prevented through proper maintenance and regular inspection. Their studies show that understanding common problems helps vehicle owners maintain optimal tire performance and safety. Neglecting tire maintenance can lead to reduced vehicle handling, decreased fuel efficiency, and increased risk of accidents.
The International Tire Safety Federation provides comprehensive guidelines for identifying and addressing tire issues before they become serious safety concerns. Their recommendations help users maintain safe and efficient tire operation. Implementing a regular tire maintenance schedule and staying alert for signs of potential problems can greatly extend tire life and ensure optimal vehicle performance.
Can pneumatic tires go flat and how can flats be prevented?
Flat tires represent one of the most common issues faced by pneumatic tire users. Understanding prevention and management strategies is essential:
- Regular Pressure Checks: Maintain optimal inflation
- Visual Inspections: Identify potential hazards
- Proper Load Management: Avoid overloading
- Road Hazard Awareness: Minimize risk exposure
- Quality Maintenance: Address issues promptly
Key prevention strategies include:
Prevention Method | Implementation | Benefit |
---|---|---|
Pressure Monitoring | Weekly checks | Early detection |
Rotation Schedule | Regular service | Even wear |
Alignment Control | Periodic checks | Extended life |
Road Assessment | Careful driving | Damage prevention |
Quality Selection | Proper specification | Reliability |
Preventing flat tires requires a combination of regular maintenance, careful driving, and proper tire selection. Maintaining optimal tire pressure, performing regular inspections, and avoiding road hazards can greatly reduce the risk of flats. Additionally, selecting high-quality tires that are appropriate for the specific vehicle and application can help ensure reliable performance and minimize the occurrence of flats.
What causes uneven wear on pneumatic tires?
Uneven tire wear can significantly impact performance and safety. The Vehicle Safety Research Center identifies several key factors contributing to irregular wear patterns:
Improper inflation pressure
Inflation pressure plays a crucial role in tire wear patterns:
Pressure Issue | Wear Pattern | Performance Impact |
---|---|---|
Under-inflation | Edge wear | Reduced handling |
Over-inflation | Center wear | Compromised grip |
Uneven pressure | Spotty wear | Irregular performance |
Fluctuating pressure | Mixed patterns | Inconsistent handling |
Chronic low pressure | Sidewall damage | Structural weakness |
Maintaining proper tire inflation is essential for preventing uneven wear and ensuring optimal tire performance. Under-inflation can cause excessive wear on the tire edges, while over-inflation can lead to center wear and reduced traction. Regularly checking and adjusting tire pressure can help maintain even wear patterns and extend tire life.
Misalignment
Vehicle alignment significantly affects tire wear patterns and performance:
- Toe Misalignment: Creates feathered wear
- Camber Issues: Causes edge wear
- Caster Problems: Affects handling stability
- Combined Misalignment: Results in complex wear
- Dynamic Alignment: Influences high-speed behavior
Proper vehicle alignment is critical for preventing uneven tire wear and maintaining optimal handling characteristics. Misalignment can cause tires to wear unevenly, leading to reduced performance, decreased fuel efficiency, and increased risk of tire failure. Regular alignment checks and adjustments can help ensure even tire wear and extend tire life.
How often should pneumatic tires be inspected and maintained?
Regular inspection and maintenance schedules are essential for optimal tire performance and safety. The Professional Tire Industry Association recommends specific maintenance intervals:
Checking tire pressure
Proper pressure monitoring involves systematic checks:
Check Frequency | Conditions | Actions Required |
---|---|---|
Weekly | Normal use | Basic inspection |
Before long trips | Extended travel | Thorough check |
Temperature changes | Seasonal | Adjustment needed |
Heavy loads | Special use | Extra monitoring |
After impacts | Incident response | Damage assessment |
Regularly checking tire pressure is one of the most important aspects of tire maintenance. It is recommended to check tire pressure at least once a month, as well as before long trips or when carrying heavy loads. Seasonal temperature changes can also affect tire pressure, so it is important to check and adjust pressure accordingly. After any impacts or incidents, tires should be thoroughly inspected for potential damage.
Rotating tires
Tire rotation helps ensure even wear and optimal performance:
- Regular Schedule: Every 5,000-8,000 miles
- Pattern Selection: Based on drive type
- Position Recording: Track rotation history
- Wear Assessment: Monitor patterns
- Balance Check: During rotation service
Regularly rotating tires is essential for promoting even wear and extending tire life. The specific rotation pattern and frequency may vary depending on the vehicle type and driving conditions, but a general guideline is to rotate tires every 5,000 to 8,000 miles. During rotation, tires should also be inspected for wear patterns and balanced to ensure smooth operation.
Inspecting for damage
Regular damage inspection helps prevent serious issues:
Inspection Area | Check Points | Action Items |
---|---|---|
Tread Surface | Wear patterns | Document changes |
Sidewalls | Cuts/bulges | Assess severity |
Bead Area | Seating condition | Verify integrity |
Valve Stems | Seal condition | Replace if needed |
Inner Liner | Internal damage | Professional check |
Performing regular inspections is crucial for identifying potential tire damage before it becomes a serious safety issue. Key inspection areas include the tread surface, sidewalls, bead area, valve stems, and inner liner. Any abnormalities, such as uneven wear patterns, cuts, bulges, or damage to the valve stems, should be promptly addressed. If internal damage is suspected, a professional inspection may be necessary. Catching and addressing tire damage early can help prevent more serious and costly issues down the road.
Final Thoughts
Pneumatic tires have revolutionized the way we travel, providing unparalleled comfort, safety, and performance across a wide range of applications. From the early days of John Boyd Dunlop’s invention to the advanced technology found in modern tires, the evolution of pneumatic tires has been driven by a constant pursuit of innovation and improvement. Today, pneumatic tires are an integral part of our transportation infrastructure, enabling vehicles of all types to operate efficiently and safely on roads around the world.
The science behind pneumatic tires is a fascinating blend of engineering, chemistry, and physics. The complex structure of these tires, with their layers of specialized materials and carefully designed tread patterns, allows them to adapt to changing road conditions, provide reliable traction, and absorb shocks and vibrations. The ability of pneumatic tires to distribute weight evenly and maintain their shape under heavy loads is a testament to the ingenuity and expertise of tire manufacturers and researchers.
As we move into the future, the development of pneumatic tires shows no signs of slowing down. Advancements in materials science, manufacturing processes, and digital technologies are paving the way for even more sophisticated and efficient tires. From self-sealing compounds and smart sensors to eco-friendly materials and advanced tread designs, the future of pneumatic tires is filled with exciting possibilities. As the demands placed on our transportation systems continue to grow, the role of pneumatic tires in ensuring safe, comfortable, and sustainable mobility will only become more important.
However, realizing the full potential of pneumatic tires requires a commitment to proper maintenance and care. Regular inspections, tire rotations, and pressure checks are essential for ensuring optimal performance and extending tire life. By staying informed about the different types of tires available and selecting the right tire for each application, vehicle owners and operators can maximize the benefits of pneumatic tires while minimizing the risk of failures and accidents. Ultimately, the success of pneumatic tires relies on a collaborative effort between manufacturers, regulators, and users to prioritize safety, efficiency, and innovation in tire design and maintenance.
In conclusion, pneumatic tires have transformed the way we travel, enabling vehicles of all types to operate safely and efficiently on roads around the world. From their humble beginnings as a solution to the discomfort of solid rubber tires to their current status as high-tech marvels of engineering, pneumatic tires have come a long way. As we look to the future, the continued evolution of pneumatic tire technology promises to bring even greater improvements in performance, safety, and sustainability. By understanding the science behind these tires and committing to proper maintenance and care, we can ensure that pneumatic tires will continue to play a vital role in our transportation systems for generations to come. So the next time you hit the road, take a moment to appreciate the incredible technology that keeps you rolling smoothly and safely – the pneumatic tire.